Test Protocol for Windshield Repair Systems
Test Protocol for Windshield Repair Systems
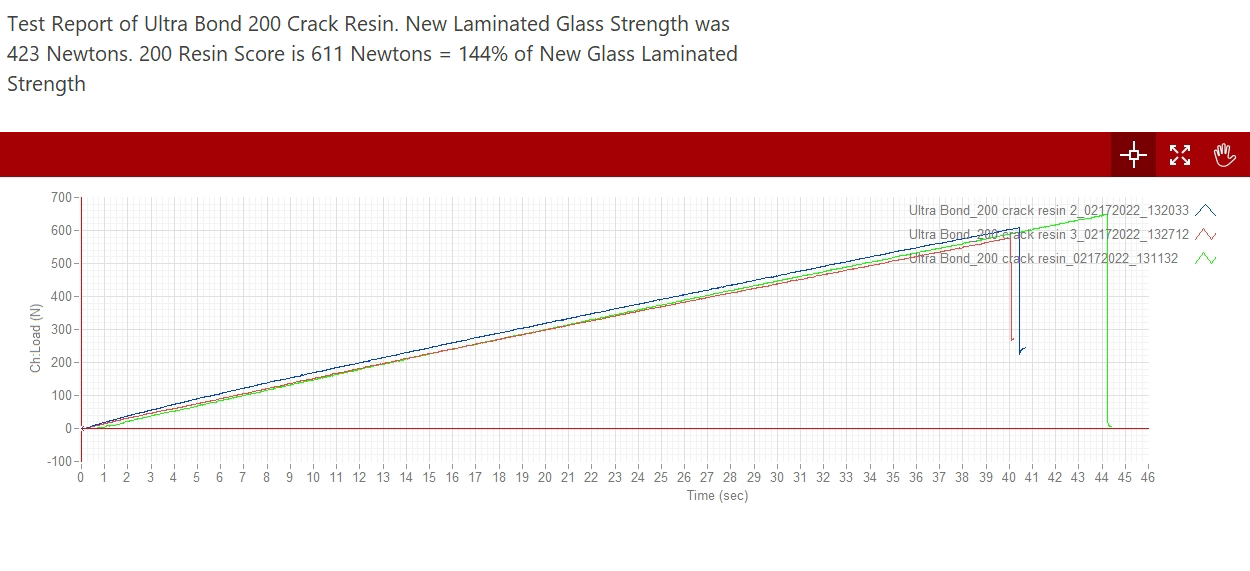
Windshields are covered by insurance. Insurance Companies are bound by their contract with their policyholder to be “Made Whole” by restoring their vehicle to its pre-loss condition.
The purpose of this test protocol is to test a windshield repair system to make a determination of its strength restoration as it compares to new laminated auto glass. This test score would then determine whether it meets the auto insurance industry’s contractual obligation to the consumer for an insurance claim.
Test Method- Windshields (float glass), Annealed Glass (windshields), Laminated glass (windshields), like other materials, undergo testing to evaluate their mechanical properties. The strength tests used by all glass manufacturers for all glass products are the “Standard Test Method for Strength of Glass by Flexure”, such as ASTM C158 and ASTM D790, which provides insights into how materials behave under uniaxial bending stress (both tension and compression). These tests provide crucial information for ensuring the safety and reliability of automotive glass. This is the only test that can reveal the restoration strength of a windshield repair system for the determination of meeting pre-loss condition.
Definition of a Repair System
A Repair System consists of 4 parts: (1) tools(s), (2) resins(s), (3) method(s) and (4) curing. The tests involve: (A) laminated glass, (B) a star-break, combination-break or crack in laminated glass, (C) the manufacturer’s custom windshield repair tool(s), (D) method(s) to assist or to completely fill when the tool cannot and (E) recommend cure (method, source, and intensity). Any new parts, updates, or changes with the system such as the tool, resin or curing must be retested.
Note: Other adhesive or resin tests that do not encompass; 2, 3, 4, A, B, C, D and E such as: compressive shear, cleavage or tensile tests etc. are not considered to be valid tests to determine restoration to meet per-loss condition for an insurance claim.
Test Samples
Glass
Laminated AS-1 type, 5-6 mm total thickness.
All test samples must be cut from the same piece/batch of laminated glass. Before starting each sample should be permanently marked to identify the product being tested by using the initials of the manufacturer/system, tool, resin and cure and then 1, 2 and 3.
Preparation of the samples - The company or person preparing the samples for testing must video tape the entire process, so it identifies the tool, resin and curing of each sample preparation.
Optical / Visual Inspection – A photograph of all three repaired pieces against a white background. For chips, take additional photographs against a white background (1) before repair, (2) after repair and (3) after thermal cycling of all samples from 4 inches, zoomed at 4 X for chip repairs. For the crack test the photographs are taken at the profile of the crack (45-degree angle) from 5 inches at 1X.
After repair, all samples must meet sections 9,11 and Annex A of the ROLAGS Standard to go any further in the testing. If the sample repaired does not meet the ROLAGS optical criterion then the system has failed, the test.
After the repair has passed visual inspection, take the 3rd photograph of the repairs after thermal cycling to make a comparison.
Tester and Preparer - can be an independent lab or in-house lab with a certified machine, both accompanied by an affidavit that the preparer did not rig or cheat the testing in any way whatsoever, stating that, “I declare that, to the best of my knowledge and belief, the information herein is true and complete. I understand this statement may be used as evidence in court and is subject to penalty for perjury.
Repairs
Chips – Star-Break or Combination break
• minimum diameter of 0.6 in (15 mm)
• maximum diameter as allowed in clause 6 of this standard.
• repaired according to the directions of that system.
• located in the geometric center of test glass.
Crack Repairs – Edge to Edge crack across the width and centered on the length.
For Chip Repairs
At least a 6-inch x 12-inch (102 mm x 305 mm) test glass with a repaired star or combination break running across the width and centered on the length.
For Crack Repairs
A 12-inch (305-mm)-long test glass with a width of 6 inches (150 mm). The repair shall be performed edge to edge across that width and centered on the length. Using a glass cutter make a straight one inch cut at one edge and then split by hand to go straight across to the other edge.
Tests
EXPOSURE /WEATHERING
Test 1 - Resistance to Thermal Cycling
Unrepaired Breaks/Chips (Star-Breaks, Combination Breaks etc.) in windshields crack-out from temperature extremes and sudden temperature changes. That is why resistance to thermal cycling is the most realistic form of exposure to test windshield repair systems. Inefficient repairs will break down from thermal stress.
Chip Repair Systems
Use three repaired glass samples of a star or combination break. The legs of the combination breaks shall extend past the bullseye portion of the break.
Take a head-on photograph against a white background of all repaired samples from 4 inches, zoomed at 4 X. Before and after thermal cycling.
Crack Repair Systems
Use three samples of crack repairs, as specified to evaluate crack repair systems. Take a photograph with a white background at the profile of the crack (45% angle) of all three repaired samples from 5 inches at 1 X. Before and after thermal cycling. Place a ruler at or on the crack so the camera can focus on the crack.
Apparatuses
a) Freezer
b) Oven
c) Lazor digital thermometer capable of reading at least -20°F (-18°C) to 300°F (150°C).
Procedure
a). Place the three repaired samples in the freezer set to bring the glass to -10 F for at least 6 hours.
b). Remove the samples from the freezer and immediately place into (not-preheated) oven set for 180 F immediately after setting the samples in the oven for 2 hours.
c). Remove samples from oven and let glass cool until 90-100 degrees F and then place back into the freezer.
4). Repeat for three rounds.
Expected Results
In addition to meeting the criteria of the ROLAGS standard section 9, 11 and Annex A, the repair should remain unchanged. The star portion shall not separate from the glass or the PVB. No refraction or voids shall appear in the bullseye or legs.
Retesting
If one test piece fails to conform another set of three like samples shall be tested. This may be repeated for a maximum of one round. If in each round of tests, a sample fails to meet the success criteria, then the resin system used is considered not to conform to the requirements of Resistance to Thermal Cycling Test as regards to that type of repair.
Recommendation- another Annex (like Annex A) of pass and fail photos.
Standard Test Method for Strength of Glass by Flexure
Test 2 - Mechanical Strength by Three-Point Bend (ASTM D790)
Glass Samples - All Test samples must be cut from the same piece/batch of laminated glass. All repairs and bend tests are done with the glass at the same temperature of 70 degrees F.
Control Number - Test three undamaged samples for the Control Number in Newtons.
New Glass
Test three samples of the new glass for the control number to compare the repaired samples restoration percentage as it compares to new glass in Newtons.
Chip Repair
Use three samples of chip repairs to evaluate a chip repair system.
Crack Repair
Use three samples of crack repairs to evaluate crack repair system.
Method
Test all three repaired samples after Resistance to Thermal Cycling.
Perform Testing for Mechanical Strength by 3-Point Bend ASTM D790 with the repaired side down, as described in the ROLAGS 2020 Annex C section C.4.3.2.2 Test A5.8 from AS/NZS 2366.2:1999, on all samples.
Expected Results
These results apply to samples tested after Resistance to Thermal Cycling.
Chip Repair Systems
At least 100% of the mean force required to produce cracks in new/ undamaged test pieces.
Crack Repair Systems
At least 120% of the mean force required to produce cracks in new/undamaged test pieces.
Exception for two sections of a crack - the Point and the Impact Break.
The impact break and the drilled hole and tapped bullseye at the point of a crack can be repaired with any resin (chip or crack) with a score of at least 100%.
Retesting
If one test piece fails to conform, another set of three like samples shall be tested along with three new glass samples. The score is then the average of the six new glass samples versus the six repaired samples. If the now 6-sample average score fails to meet the success criteria, then the system used is considered not to conform to the requirements of restoring to pre-loss condition for an insurance claim.
Test Score Exceptions – Glass fails but not the repair and the score is lower than the control number but in the range of the three new glass samples.
When both layers of glass break at once or the repair is still intact, or the glass breaks away from the repair and the score for that sample is lower than the control number the score is adjusted for a chip to 100% and 120% for a crack.
Submitted to the Auto Glass Safety Council, ROLAGS 2 Committee by
Richard Campfield, Ultra Bond, Inc.
April 2024
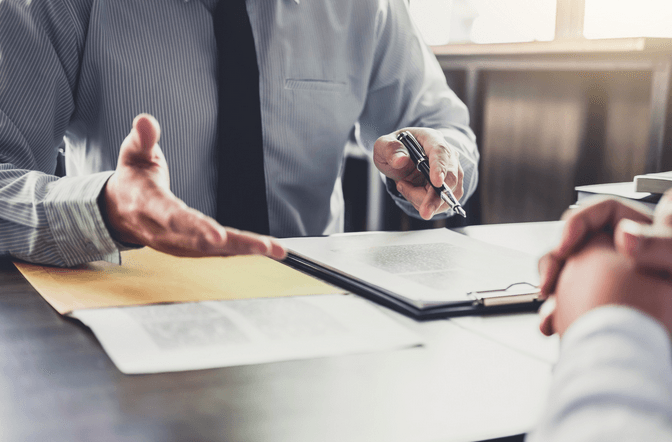
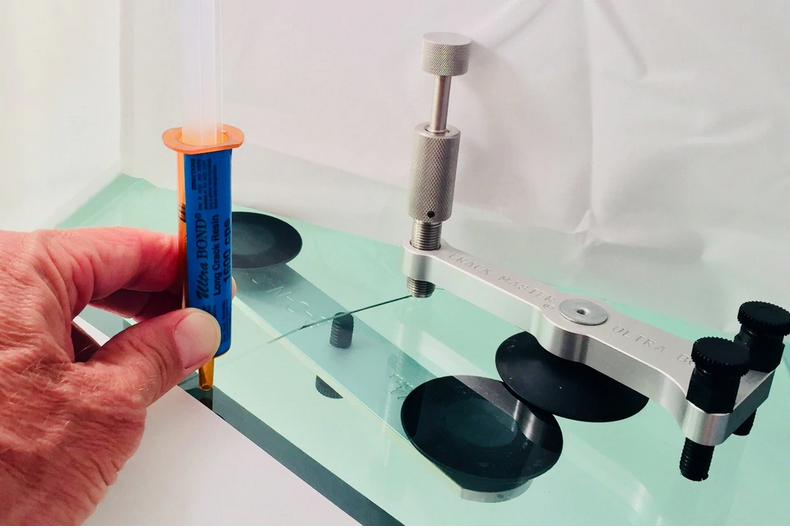